
LOVELLS
SPRINGS & SUSPENSION – AN AUSSIE ICON in the
suspension industry!
Lovells Springs
founder George Lovell, began his own company
with his three sons in Sydney way back in 1930.
George and his sons manufactured their own
spring making equipment including furnaces and
forming equipment and as a result of hard work,
Australian ingenuity and determination the
business flourished. Lovells Springs &
Suspension has long since cemented their
reputation as a world leader, manufacturer and
supplier of premium quality springs, shocks and
suspension components to suit a broad range of
applications for automotive, 4x4, agriculture,
mining and Aussie railway industries.
Lovells Springs & Suspension is now in its 79th
year of business as a manufacturer and supplier
of premium quality springs, shocks and
suspension components. The company, has built an
enviable reputation worldwide as a specialist
Australian manufacturer to bring you a range of
suspension products that offer you “The Ride of
your Life”
LOVELLS
SPRINGS AUSTRALIAN MADE COIL SPRINGS
Lovells Coil Springs are designed as a superior
performance replacement part for mass-produced
O.E (Original Equipment) coil springs, they
exceed original ratings by 10% - 50% (depending
on the application), thus handling is
dramatically improved and many ride height
variations are available for most makes and
models. Lovells coil springs are all
manufactured to the highest standard in
Australian Made OneSteel micro alloy steel in
Newcastle, NSW.
Many Lovells coil springs are of progressive
rate design. This design enables the spring to
increase in spring rate when you need it and
decrease when you don't, insuring the ultimate
in handling and ride comfort.
All heating and tempering furnaces are
electronically controlled to precise
temperatures. Each individual spring is hot
coiled on a variable speed PLC (Programmable
Logic Controlled) coiling machine. After oil
quenching and tempering, the springs are rate
tested on a sample basis and scragged solid to
achieve the maximum fibre stress.
The springs are then shot peened ready for
protective surface finishing, prior to powder
coating. After final inspection the springs are
packaged in protective cardboard boxes ready for
warehousing or despatch.
The company’s philosophy of “Up to standard, not
down to a price” paired with a commitment to
customer satisfaction and continuous
improvements provide the basis for the quality
of products, as well as the quality of the
business relationships developed with their
clients.
Materials
All spring steel used in the manufacture of
Lovells Springs is sourced from OneSteel
(previously BHP) to AS1447-1991 (Unless
specified otherwise). Spring steels used include
silicon manganese, silicon chrome, carbon chrome
and other micro alloy spring steels.
R & D Research and Development
Lovells have gained a reputation as being at the
forefront of spring design and manufacturing
techniques as well as high quality suspension
components by committing to the finest quality
materials available, skilled staff, computer
spring design and test equipment, PLC
(Programmable Logic Controlled) manufacturing
equipment and extensive road and race tested
products to ensure "THE RIDE OF YOUR LIFE"
Lovells springs are designed on advanced
computer aided programs and sophisticated in
house test machines, before extensive road
testing and performance checks to ensure the
ultimate performance of the product.
Lovells initially carry out an evaluation of a
vehicle via road testing, components analysis
and performance and specifications examination.
Road testing involves driving a vehicle over
many types of terrain, with and with out loads
before subjective judgement is made on how
Lovells could improve the performance of the
vehicle in terms of ride height, handing, load
carrying capacity (up to the manufactures
recommended GVM). Suspension systems are then
designed as a combination to ensure springs
rates, suspension travel and handling compliment
our shock absorber controls and other
components. Performance including load-carrying
capabilities versus ride comfort is also taken
into consideration. Engineering samples are left
on a vehicle for durability testing for a period
up to 12 months.
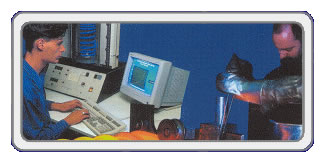
Manufacture
Lovells Coil Springs are manufactured in
accordance with ISO9002 to the highest standards
in our own modern manufacturing facilities.
Lovells Coil Springs are manufactured to exceed
the appropriate Australian Standards using
OneSteel (previously BHP) micro alloy spring
steels supplied to AS1447-1991. All heating and
tempering furnaces are electronically controlled
to precise temperatures. Each spring is
individually hot coiled on a variable speed PLC
(Programmable Logic Controlled) coiling machine.
After oil quenching and tempering, the springs
are rate tested on a sample basis and scragged
solid to acheive the maximum fibre stress.
The springs are then shot peened ready for
protective surface finishing, prior to powder
coating. After final inspection the springs are
packaged in protective cardboard boxes (unless
specified otherwise) ready for warehousing or
dispatch.
Quality
The finished quality of the Lovells product
reflects quality workmanship by skilled people
using top quality materials, manufacturing
processes and inspection equipment. Lovells go
to great lengths to ensure their products are of
the highest quality. All of the Lovells range is
manufactured and inspected in accordance with a
documented Lovells Quality standard. Management
is based on the principles of the ISO9002
standard. All springs are manufactured in
accordance with the appropriate Company,
Customer and/or Australian standards. The
Company's commitment to research and development
ensures that only the latest technology is used
in the manufacture of its product.
Lovells Springs achieve improvement in the
following areas:
-
Ride Height
To restore the vehicle to its original
standard ride height, when the original
springs have sagged or weakened. To lower the
centre of gravity of the vehicle for enhanced
appearance, performance and handling
characteristics. To raise the vehicle for
increased ground clearance and load carrying
capabilities eg. Towing LPG ( load bearing
accessories).
-
Handling
Lovells Springs ratings exceed that of
original equipment springs by 10% - 50%
(depending on the application), therefore
handling is dramatically improved by
controlling excessive body roll and brake
dive.
-
Load Carrying
Lovells offer a range of heavy-duty uprated
coil and leaf springs to increase the
vehicle's load carrying capabilities and
maintain stability when laden. These springs
should be selected where a vehicle carries
heavy loads, is used for towing, is fitted
with LPG or larger fuel tank or Load Bearing
Accessories ie. bull bar, winch, roof racks
etc.
-
Comfort
Lovells Springs offer a range of variances in
progressive and linear rate coil spring
design, ratings and ride height options to
enable the vehicle to be enhanced to the
customers exacting comfort requirements.
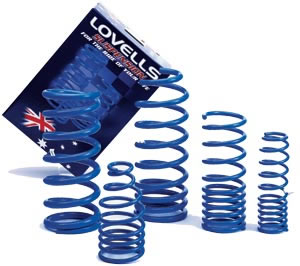
Warranty
5 YEAR / 100,000k WARRANTY !
COIL SPRINGS Installation Tips – A Guide
only!
-
Measure your vehicle's ride height before
installing Lovells Springs. This will ensure
you know the amount of lowering after
installation. On a level surface, measure from
the upper wheel rim to the highest point of
the fender well, before installation and
after. And before you measure 'after'
dimension, drive the car hard for ten miles to
let the springs, spacers, etc. settle
properly.
-
Before removing springs from your car, put a
sequential number mark on each component, from
top to bottom. This will help you reassemble
the new and existing parts in correct order.
-
Before disassembling the strut assembly, draw
a vertical line with a marker across each
component. This will help you reinstall all
the OE parts with the original factory
orientation.
-
Mark the position of all alignment-related
mounting bolts. This allows a good starting
point for the post-installation alignment.
-
Work on one corner of the car at a time. Some
OE strut assemblies have up to 10 pieces which
must be assembled in the exact order in which
the factory installed them. Disassemble one
corner, and if you make a mistake or lose
track of the order of assembly, you can refer
to the corresponding assembly as a reference.
-
Reinstall all bolts in the same orientation
(up or down) in which the manufacturer
installed them.
-
Mark parts to indicate left and right side
before removal. Many parts are designed
specifically for the left or the right side of
your car.
-
Note any protective tubing on the factory
springs, and the locations. Lovells springs
are designed to reuse all factory tubing and
isolators to prevent noise and premature wear.
-
Many struts on front-wheel-drive cars have a
steering bearing located between the chassis
and upper strut mount. Note the orientation
and be sure not to contaminate or disassemble
the bearing. Proper care must be taken to
ensure this bearing is installed exactly as
the factory installed it to prevent steering
noises and premature wear of related steering
components.
-
Brake lines and anti-lock brake sensors: Note
the routing and mounting positions of all
wires, cables and brake lines. Reinstalling
the links differently from the factory
position can result in damage or brake
failure.
Support the spindle and brake assemblies with
wire, wire coat hangers or welding rod.
Failure to support the spindle may allow the
inner axle to disengage from the transmission.
-
Do not let the brake calliper or spindle hang
on the brake line. This may damage the brake
line and cause premature wear or even failure
of the line.
-
Always use the proper spring compressor to
remove springs from your car, or when
disassembling a strut. Springs store an
enormous amount of energy and can seriously
injure you or someone else if this energy is
released unexpectedly.
-
Leave 1/4" to 1/2" space between the end of
the coil and the spring seat pocket. This will
help prevent spring noise when encountering
large bumps.
Please use the "Shop By
Vehicle" list in the LHS column of our Home Page
for your application
If you don’t find them listed for your
vehicle as yet, give us a call or email us!